Rice bran oil refining machine adopts physical refining process, which greatly reduces the rice bran oil production costs. Rice bran oil refining machine of Henan Huatai Oil Machinery is mainly used in different vegetable oil refining process plant. It has high refining rate and continuous process, and can refine different vegetable oils, such as: soybeans, peanuts, cottonseed, rapeseed, corn, etc. It is suitable for all oil-containing plants.
Rice bran crude oil contains free fatty acids, bran wax, phospholipids, proteins, and pigments. As edible oil, it needs further purification and refining to remove these impurities.
The rice bran oil refining equipment process is as follows:
Crude rice bran oil → impurity removal → wax removal → hydration → alkali refining → water washing → dehydration → deodorization → refined rice bran oil
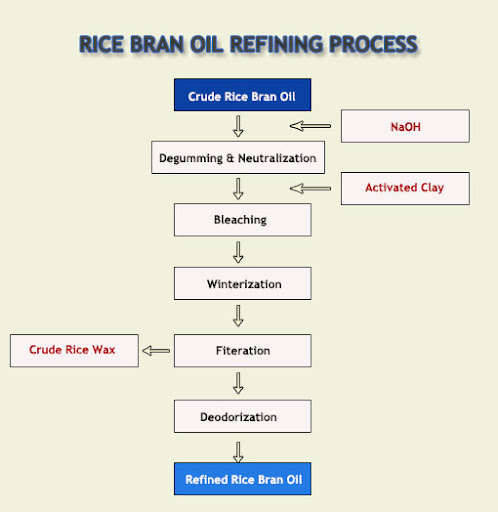
rice bran oil refining process
1. Impurity removal—To heat rice bran oil to 90°C and filter it with a filter press.
2. Wax removal – The wax content in rice bran oil is generally 3%-5%. Bran wax cannot be absorbed by the human body and has no edible value. It must be removed to avoid affecting the quality of rice bran oil.
3. Hydration – First heat the crude rice bran oil to 65-70°C, then add hot water at the same temperature equal to 5% of the oil while stirring, stir for 40-60 minutes, and stop heating when the temperature rises to 80°C. Stir for another 25 minutes or so and let rest for 4-6 hours.
4. Alkali refining – before alkali refining, measure the acid value of crude rice bran oil and calculate the amount of alkali added according to the following formula:
Dosage of solid alkali (kg) = quality of rice bran oil (t) X acid value X 0.713
In the formula, 0.713 is the ratio of the molar masses of sodium hydroxide and potassium hydroxide.
Then prepare a dilute alkali solution of 18~20oBe, and send the hydrated rice bran oil into the alkali refining tank. When the soap particles appear obviously, the steam is heated up (1℃/min), and the oil and soap particles are obviously stratified. Stop heating, the final temperature does not exceed 80°C, reduce the stirring speed to 40r/min, and add hot salt water with a concentration of 3%-5%. When the soap particles turn gray-black and have sunk, stop adding salt water and continue stirring for 10min to let it sit for a few minutes. When all the soap stock sinks to the bottom and the oil becomes a thin paste, release the soap stock.
5. Water washing – To heat the alkali-refined rice bran oil to 80~94℃, add boiling water with 10%~15% oil content while stirring, stir for another 15 minutes, and let it stand for 1~2 hours. If the pH value of waste water at this time is close to 7, it can be drained; if the wastewater still shows red after the phenolphthalein test, it needs to be washed until the phenolphthalein test does not show red or the pH meter shows neutral.
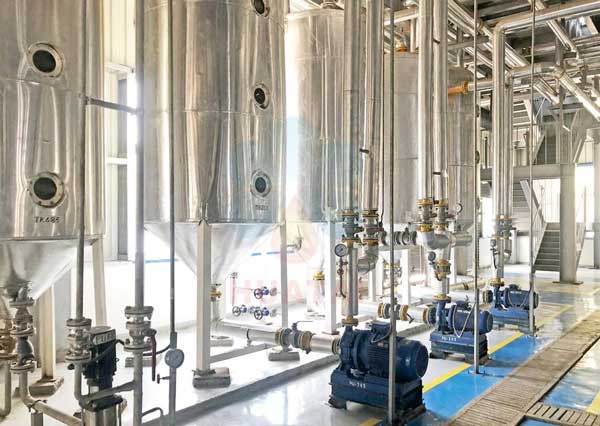
rice-bran-oil-refining-machine
6. Dehydration – To heat the oil to 105~110℃ and stir until no foam appears on the oil surface. The moisture content of the dehydrated rice bran oil should be less than 0.2%.
7. Decolorization—To heat the oil to 95~100℃, and add dry activated carbon or acidic clay while stirring. The added amount is about 2% of the weight of rice bran oil. After stirring for 0.5 hours, take a sample and observe it. If it meets the standards, you can enter the next process. Otherwise, you still need to repeat decolorization several times until the oil turns yellow and translucent.
8. Deodorization – To mainly remove oxides in oil, such as ketones, aldehydes, free acids and sulfur-containing compounds. These substances exist inrice bran oil and give the oil a special “odor”, so they should be removed. Deodorization is usually carried out by passing superheated steam under vacuum (i.e. 60mmHg) to raise the oil temperature to above 220°C, processing for 4 to 6 hours, then lowering the oil temperature to 40 to 60°C, and transferring it into the cooling oil tank. Cool to obtain refined rice bran oil.
The quality standards of refined rice bran oil are: orange and transparent in color, no rancidity or odor, moisture content below 0.2%, impurities below 0.3%, and an acid value of 5mgKLH/g.